Which is the Best Industrial Floor Paint for Concrete?
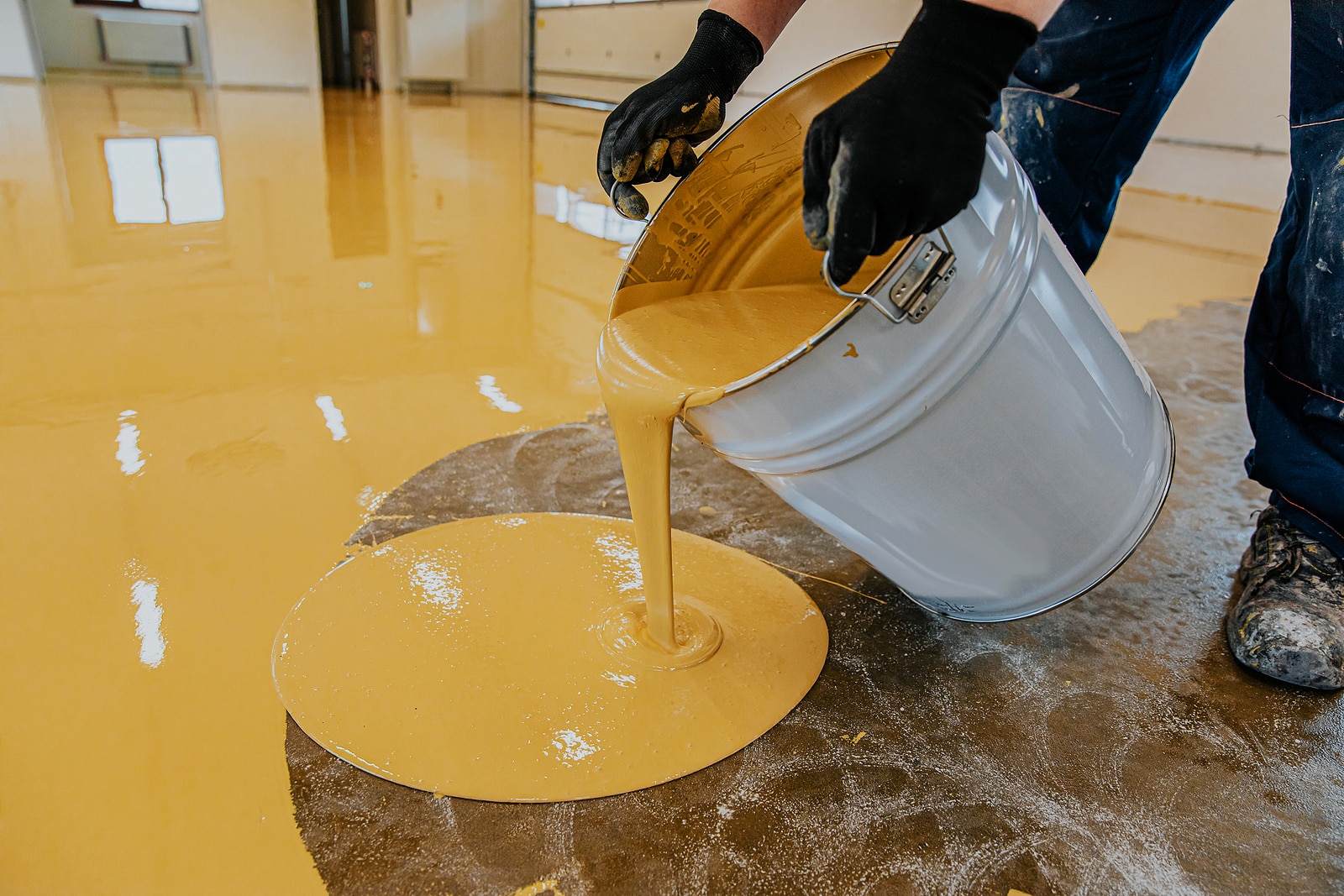
When it comes to industrial settings, warehouses, and commercial garages, bare concrete floors simply don’t cut it. Not only do they look uninspiring, but they’re also harder to maintain and keep clean. The right industrial floor paint for concrete transforms these spaces into professional, durable environments that can withstand the toughest conditions while remaining easy to maintain.
Understanding Industrial Floor Paint Options
Industrial concrete floor coatings must handle extreme conditions that regular paints cannot. Heavy machinery, chemical spills, constant foot traffic, and temperature fluctuations demand specialized formulations designed for maximum durability and performance.
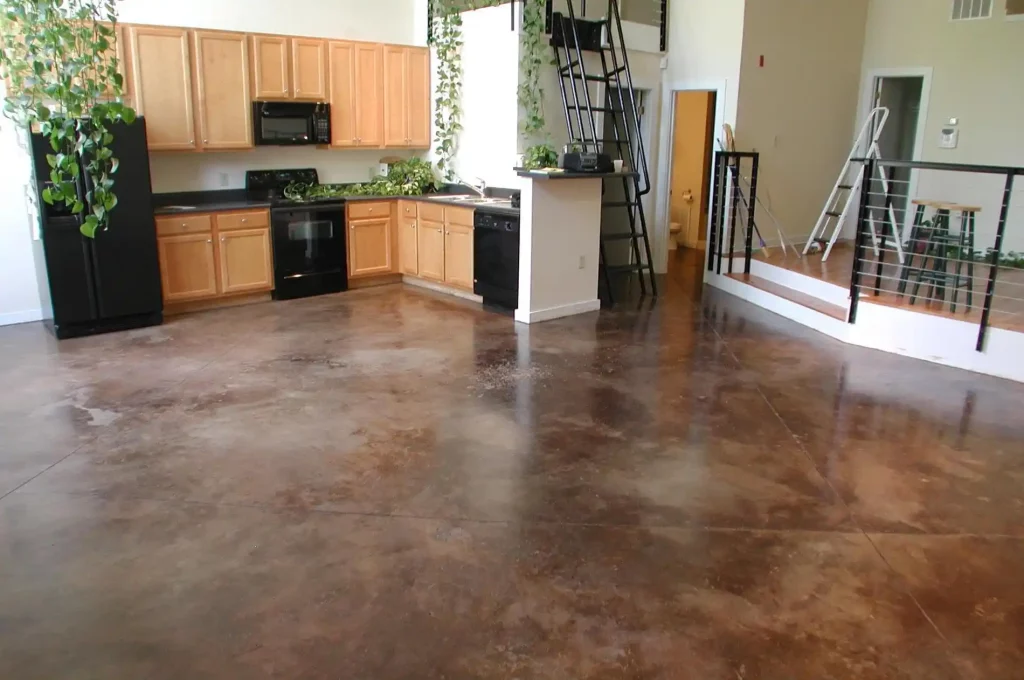
Epoxy Floor Paint: The Heavyweight Champion
Epoxy resin systems have long been the go-to choice for industrial concrete floors, and for good reason. These coatings offer unparalleled hardness and compression strength, making them ideal for facilities with heavy equipment like forklifts and industrial machinery.
100% Solids Epoxy represents the strongest option available. With no solvents or water additives, this coating provides maximum durability but comes with a significant drawback: a pot life of just 30 minutes. This short working time increases installation costs due to material waste and the need for experienced applicators.
Solvent-Based Epoxy offers nearly the same strength as 100% solids while providing extended pot life for easier application. The coating doesn’t begin hardening until the solvent evaporates, giving applicators more time to work. However, environmental and health concerns regarding VOCs are pushing many facilities toward alternatives.
Water-Based Epoxy addresses environmental concerns by reducing VOC content, but it’s the weakest of the epoxy family. While suitable for office and laboratory environments, it cannot withstand the harsh conditions of warehouse or garage settings.
Polyurethane: The Flexible Alternative
Polyurethane floor paint for concrete represents a high-quality alternative that offers unique advantages over epoxy systems. This coating dries to a thinner coverage compared to epoxy but provides superior flexibility and impact resistance.
The flexibility of polyurethane makes it more resistant to cracking and impact damage. While epoxy’s hardness can make it brittle, polyurethane’s softer cure allows it to absorb impacts and resist scuffs more effectively. This translates to longer-lasting floors in high-traffic industrial environments.
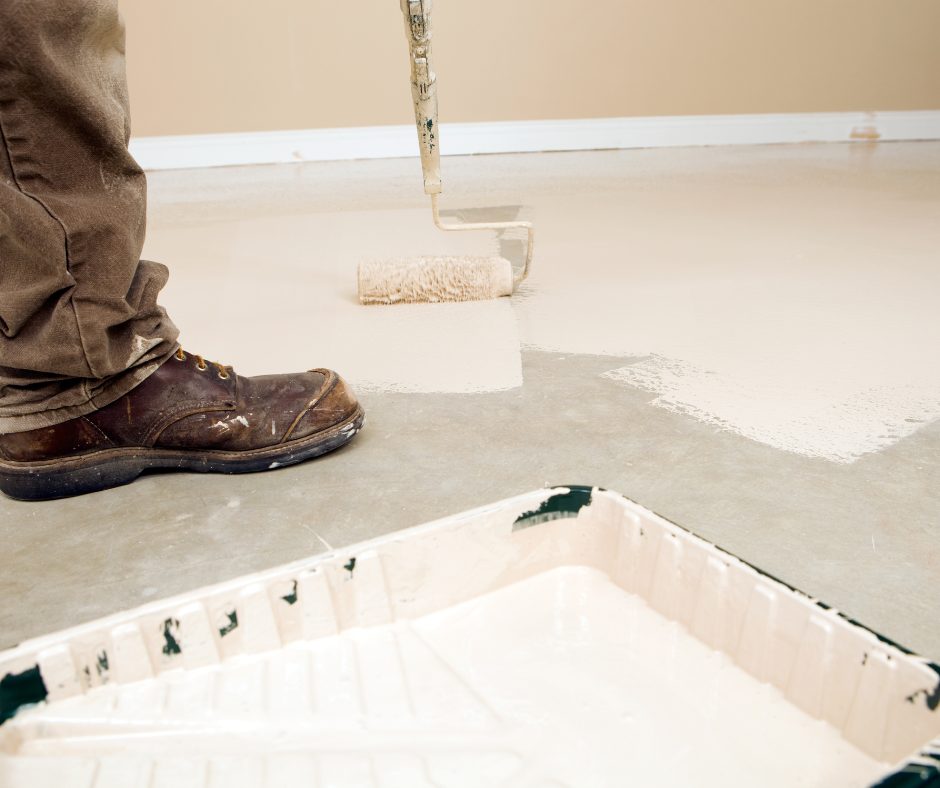
Comparing Epoxy vs. Polyurethane for Industrial Applications
Epoxy Advantages
- Superior hardness for extreme heavy-duty applications
- Lower upfront cost compared to polyurethane systems
- Excellent humidity tolerance in moisture-prone environments
- Resistance to sulfuric acid spills
Epoxy Limitations
- Shorter lifespan due to brittleness
- Limited chemical resistance to certain substances
- Long curing times that disrupt operations
Polyurethane Advantages
- Flexibility and durability resist impact and cracking
- Superior abrasion resistance handles scrapes and scuffs
- Broad chemical resistance to solvents, alkalis, and acids
- Fast curing time minimizes downtime
- Temperature tolerance performs in extreme conditions
Polyurethane Limitations
- Higher upfront cost than epoxy systems
- Poor humidity tolerance requires moisture-free application conditions
Choosing the Right Industrial Floor Paint
Selecting the optimal industrial floor paint for concrete depends on several critical factors:
- Traffic Type and Volume: Heavy forklift traffic demands different protection than foot traffic alone. Consider both the weight and frequency of equipment use.
- Chemical Exposure: Different coatings handle various chemicals differently. Assess what substances your floors will encounter and choose accordingly.
- Environmental Conditions: Temperature extremes, humidity levels, and UV exposure all impact coating performance.
- Operational Requirements: Consider how long your facility can be out of service for coating application and curing.
- Budget Considerations: Factor in both initial costs and long-term maintenance expenses when making your decision.
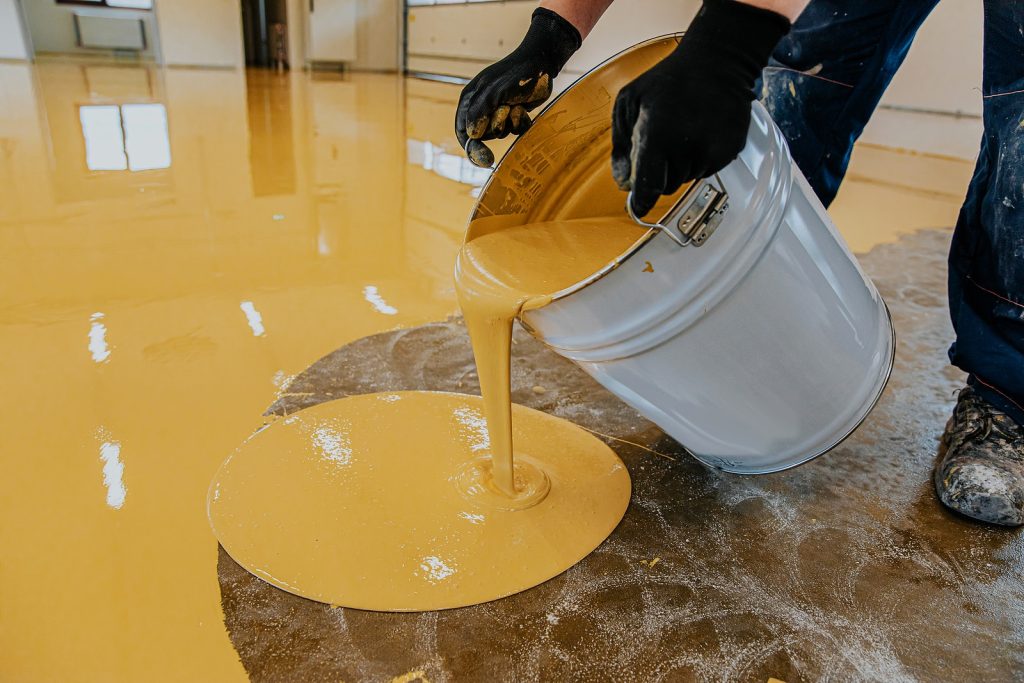
Professional Surface Preparation: The Foundation of Success
Proper surface preparation determines the success of any industrial floor paint application. This critical step cannot be overlooked, as poor preparation leads to adhesion failure and premature coating breakdown.
Essential Preparation Methods
- Basic Cleaning: Remove all loose debris, dirt, and contaminants through vacuuming or sweeping. This baseline preparation is suitable for new concrete in good condition.
- Solvent Cleaning: Cut through oil, grease, and stubborn stains using appropriate solvent cleaners. These fast-drying solutions allow for quick turnaround times.
- Degreasing: Heavily contaminated floors require specialized degreasing solutions applied according to manufacturer specifications, followed by thorough rinsing and drying.
- Acid Etching: Hydrochloric acid etching dissolves weak surface layers and opens concrete pores for better penetration. The resulting surface should have a sandpaper-like texture.
- Mechanical Preparation: Shot blasting, grinding, or scarifying provide the most effective preparation by removing existing coatings, contaminants, and weak surface layers.
Installation Best Practices
Successful industrial floor paint application requires attention to environmental conditions and proper technique. Temperature and humidity must be within specified ranges, typically 50-85°F with relative humidity below 85%.
Apply coatings in thin, even layers using appropriate tools. Multiple thin coats provide better protection than single thick applications. Allow proper curing time between coats and before returning equipment to service.
Maintenance and Longevity
Regular maintenance extends the life of industrial floor coatings significantly. Implement a cleaning schedule using pH-neutral cleaners and avoid harsh chemicals that could damage the coating. Address spills promptly to prevent staining and chemical damage.
Inspect floors regularly for signs of wear, damage, or chemical attack. Early intervention through spot repairs can prevent the need for complete recoating.
Cost-Effectiveness Analysis
While polyurethane systems typically cost more upfront than epoxy, their longer lifespan and superior performance often make them more cost-effective over time. Consider total cost of ownership, including installation, maintenance, and replacement costs when evaluating options.
High-quality polyurethane coatings can last 5-10 years with proper maintenance, while epoxy systems may require more frequent reapplication in demanding environments.
Conclusion
Industrial floor paint for concrete transforms utilitarian spaces into professional, durable environments capable of withstanding the most demanding conditions. Whether you choose epoxy for its unmatched hardness or polyurethane for its flexibility and longevity, proper product selection, surface preparation, and application techniques are essential for success.